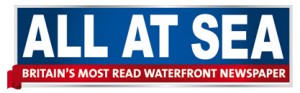
Below Water Servicing and Protection
Bill Selsey looks at the options available in the antifoul market
With the below water hull once again looking like it should do and not a flaking horror show (thank you Peelaway Marine); my attention has now been focused on how to best protect the below water areas and what products to use. The simplistic view is to apply antifouling, affix new anodes and launch. Easier said than done!
Reality poses a whole raft of very important decisions: (1) priming: do I apply a single pack vinyl primer or an osmosis prevention epoxy system, (2) antifouling: do I go for hard, eroding, copper oxide, copper thiocyanate, biocide, thin film, traditional or silicone product and (3) anodes: is the choice zinc or aluminium. Thank heavens the choice on the anodes appears far simpler and should be easier!

Jotun Non Stop II available in 2.5 ltr tins and Vinyl Primer available in 0.75 and 2.5 ltr tins
Antifouling – with over eight brands offering in excess of 40 antifouling products – my dilemma has been cutting through the ‘marketing’ blurb to make the decision on the most suitable products to use. Good job we have not got an aluminium hull with the associated issues to consider. I have used products from various global manufacturers over the past few years – one required a second mortgage to buy the product and the other I found simply did not work. So, do I go for the hard matrix non-eroding type or do I continue with the eroding products that apparently are easier to maintain over a longer period? My understanding is the hard types are better suited to power boats, sailboats in mud berths or the racing sailboat fraternity wanting to scrub, polish and buff the product to within an inch of its life. Whereas, the traditional eroding types I have been using for many years are best suited to all boats up to 25 knots. I dread the thought of my little pride and joy going into self-destruct mode at 25 knots – an average cruising speed of 5 to 7 knots; with the odd surge (hardly a surf) to 10 knots; suits us just fine!
Decision made; after weeks of discussing in the club with fellow yachties and conducting my own research it was actually a far easier decision to make than I originally thought. I decided to go for the only product currently on the market offering a nine-month guaranteed antifouling performance – Jotun’s NonStop II. I have heard of this brand over the years and seen it used in commercial yards on fishing boats around the UK. Hardly surprising with it being the largest marine antifouling brand in the UK. In all honesty I had got to the stage where I could not decide based purely on the manufacturer attributes.
All products in the premium eroding sector seem to be so similar, it stood out to me that Jotun are confident enough in their product to offer a performance guarantee. This being all the more impressive bearing in mind the products are formulated to meet the new Biocidal Products Regulation (BPR); not necessarily the case with all other brands.
With no obvious signs of osmotic blisters, but the hull not having had the time to fully dry out, I decided not to apply the multi-coat epoxy osmosis prevention scheme on this occasion. Now knowing that full antifouling removal is no longer the nightmare it used to be, I will do this in a few years’ time, slipping the boat earlier leaving her to fully dry out later into the spring.
On this occasion the decision is to go for the traditional single pack vinyl primer. It always makes perfect sense to me to follow a manufacturer recommended scheme wherever possible. Thus I’ll be using the aptly named Vinyl Primer (does what it says on the tin) by Jotun. The news just gets better – it just so happens that Vinyl Primer is very competitively priced against other similar products.
With all the major decisions made, I am only left with the anode selection. Selecting the brand will not be an issue – where possible I always go for UK manufactured products. As mentioned earlier, the only decision is do I continue with the tried and tested zinc anodes or do I venture out and go for the relatively newly introduced aluminium products. Apart from being the better option for brackish waters; where we do occasionally cruise; there are apparently many additional advantages to using aluminium anodes.
Aluminium anodes have a greater electrical potential to ‘absorb’ corrosion, corrode more slowly (another cost saving – winner!) and erode more unevenly with visible ‘craters’ providing a greater surface area.
Not being a racing sailboat or fast motor cruiser, weight is not that important to us. However to other boats weight could be quite significant. With anodes working on surface area not weight, aluminium could be a distinct advantage.
With the boat painted and all bronze seacocks stripped and cleaned, spare parts purchased and fully serviced and ready for relaunch a spanner has been thrown in the works. The local chandler has in stock a range of composite through hull skin fittings and seacocks requiring no maintenance or annual servicing! Sounds way too good to be true and will require more research for another day.
With a shopping list of Jotun’s NonStop II antifouling, Vinyl Primer, aluminium anodes and not forgetting the antifouling guarantee information I am off to my local (chandlery) to get shopping.
The post Below Water Servicing and Protection appeared first on All At Sea.